Hiki ke hoʻopauʻia nā mea hoʻokele sterper
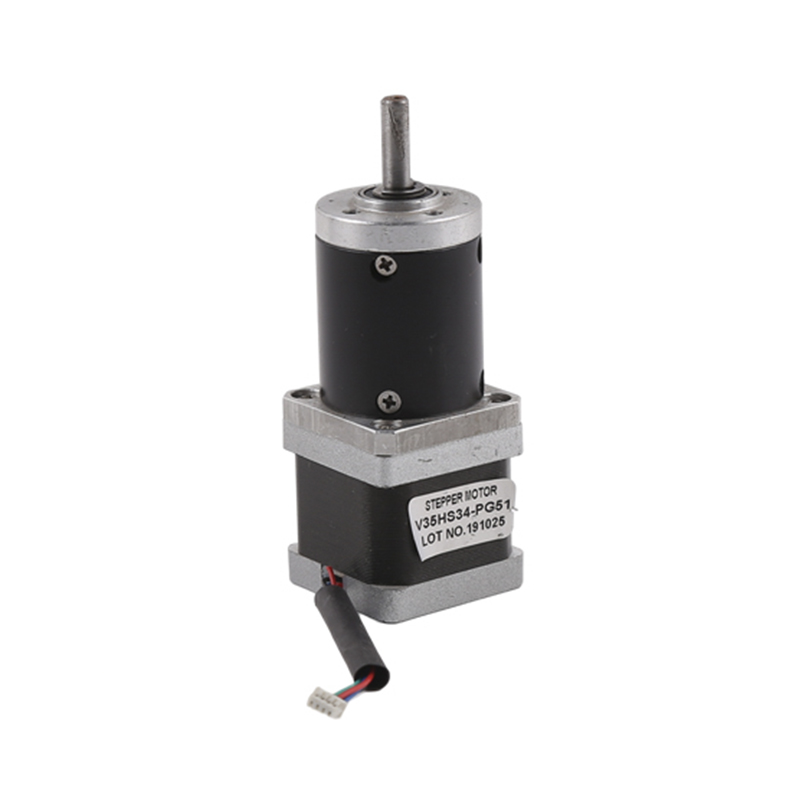
Hiki ke kiʻiʻiaʻo Steper Motor Garping e nā mea iʻikeʻoleʻia e ka paleʻana o ka mechanical,ʻaʻole lawa ka hopena o ka uila a iʻole ke kaʻaʻoleʻana i kēia manawa. I ka hoʻolālā a me ka hoʻohanaʻana i nā Motors Motors, e hoʻokumuʻia i nāʻano hana likeʻole, a me nā hana maʻamau, e pili ana i ke kaʻaʻana.
Pono e hōʻikeʻia nā kiʻi aʻe i ka wā e hoʻohana ai i nā mea hana sterips:
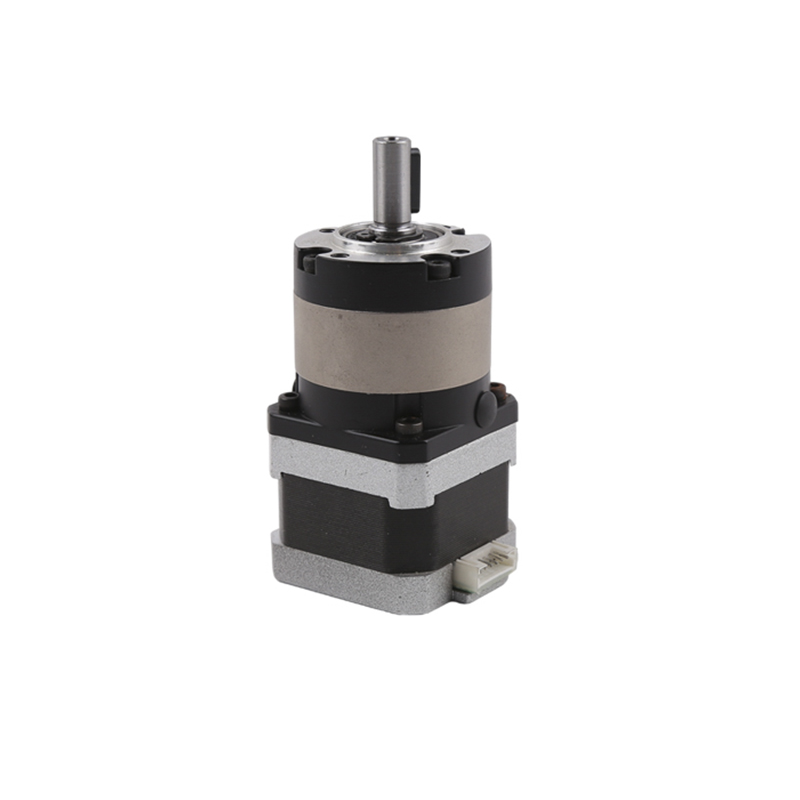
1, kūpono kūpono e hōʻemi i ka ukana o ka pahu pahu kaʻa e hōʻemi i ka hiki ke pale aku.
2, mālama pinepine a lawelawe i ke kaʻa kaʻa, e like me ka hoʻomaʻemaʻeʻana i loko o ke kaʻa a me ka lubricating i nā mea hana maʻamau.
3, ADPT HOLD HOLOHE, e like me ke kauʻana i nā polokalamu palekana overcurrent, e pili ana i nā pale pale pale ma muli o ka hoʻopauʻiaʻana o nā mea hana
I ka hōʻuluʻuluʻana, hiki i ke kaʻa kalepa ke puhi i ke kaʻa i ka hihia o kahi manawa lōʻihi e pale aku ai i ka paleʻana i nā hana pale e hiki ai ke hōʻoia i ka hana maʻamau
ʻO ka hopena o ke kaomiʻana i ke kaʻa kaʻa
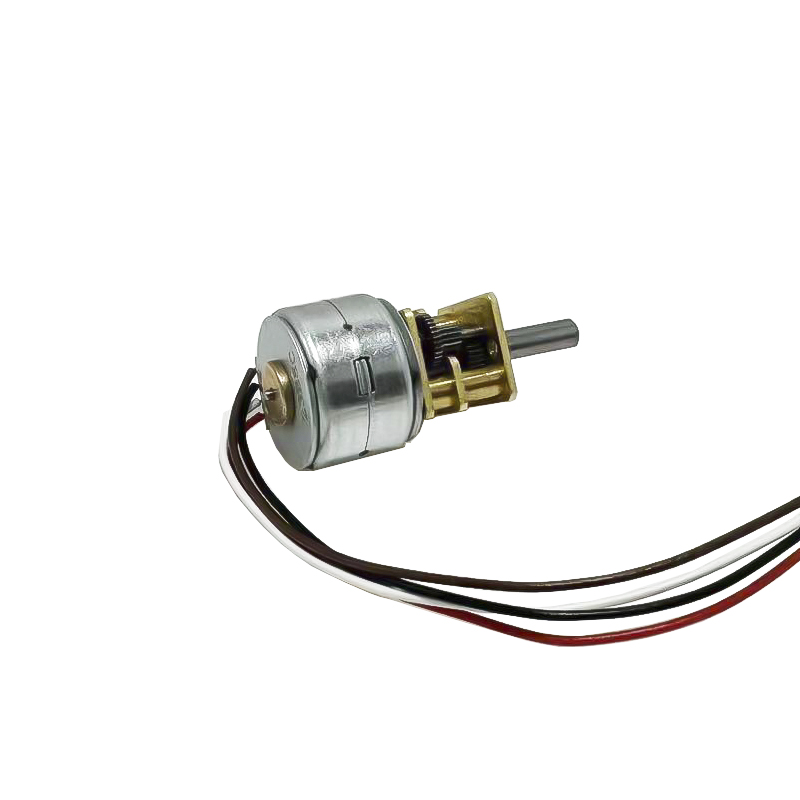
ʻO nā hopena no ka hoʻopauʻana i ke kaheʻana o ke kaʻa
1, e nānā pono inā he mea maʻamau keʻano o ke kaʻa, e nānā inā he loli ka mana o ka mana me ka uila.
2, e nānā pono inā hana ka mea hoʻokele, e like me ka mea e like me ke kūleʻa o ke kaʻa a he kūpono paha ke kaʻaʻana i kēia manawa.
3, E nānā inā he maʻamau keʻano o keʻano o ka mīkini kaʻa, e like me ka mea e like me ka libricated, a he wahi paha nā'āpana, etc.
4, e nānā inā he'ōnaehana o ka hoʻokele o ke kaʻa o ke kaʻaʻana, e like me ka hōʻailona o ka mea kūʻai aku a he maikaʻi paha ka paleʻana.
Ināʻaʻole hiki i nā kumu o nā mea i luna aʻe ke hoʻoponopono i ka pilikia, hiki iāʻoe ke noʻonoʻo i ke hoʻololiʻana i ke kaʻa a iʻole ka mea hoʻokele, aʻimi paha i ke kākoʻo loea.
Kahakaha: Ke hana neiʻo ia me ka hoʻokeleʻana i nā pilikia o ke kaʻa, mai hoʻohana i ka nui o ka uila, a hoʻokele paha i ke kaʻa, he mau mea hōʻeha a iʻole ka hopena Pono e kauʻia ma keʻano o ka hana maʻamau ma ka hanaʻana i ka pilikia,ʻike i ke kumu kumu o ka pilikia, a lawe i nā kumu kūpono e hoʻoponopono ai.
No ke aha ke hoʻololiʻole ai ka pahu pahu pahu pahu pahu pahu ma hope o ke kāohiʻana i ka rotation?
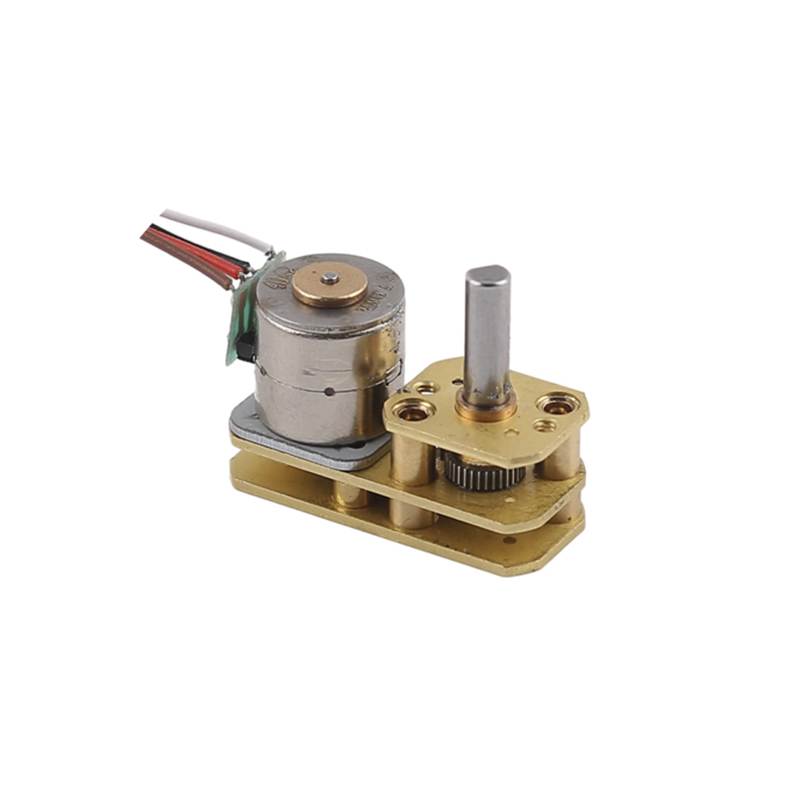
ʻAʻole ke kumu ke kumu o ke kaʻa holoʻana ma hope o ke kāohiʻana ma muli o ka hōʻehaʻana i nā kaʻa a iʻole nā hana palekana o ke kaʻa.
I ka wā e hoʻopaʻaʻia ai kahi kaʻa holo kīwī, inā hoʻomau ka hoʻokele kaʻa i ka pilikia, he nui ka wela o ka wela, e hoʻopauʻia ana, a kuni paha paha. I mea e pale aku ai i ke kaʻa mai nā pōʻino, he nui nā kaʻa kaʻa kaʻa e hoʻopiliʻia me ka hana o ka mana i loko I kēia hihia,ʻaʻole e hoʻohuli ka mīkini uila.
Eia kekahi, inā he mau mea i loko o ka pahu pahu kaʻa i hōʻikeʻia ma muli o ka paleʻana o ka lole a iʻole ka lubrication a iʻole nā mea inuʻole. Inā holo ke kaʻa no kahi manawa lōʻihi,ʻoi aku ka nui o nā mea i loko o ke kaʻa a iʻole e lilo i paʻa a iʻole a iʻole a iʻole a iʻole a iʻole. I kēia hihia, inā ua pōʻino ka bear,ʻaʻole hiki i ke kaʻa ke hoʻololi pono.
No laila,ʻaʻole i hoʻohālikelike ka mīkini hoʻokele ma hope o ke kāohiʻana, pono paha e nānā i ka hana a me nā pilikiaʻole o ke kaʻa, he hoʻoponopono paha ke kala ma keʻano o ke kumu, a inā e hana pono ke kaʻa.
Post Time: Dec-16-2024